誰もが認める良質の製品を市場に流すためには「品質」と「検査」の組み合わせは切っても切れない関係です。
検査とは一概に言っても様々な種類があり、その時求められている「検査」を実施していく事が重要となります。
今回は品質管理における検査について種類と目的、特徴に着眼してまとめてみました。
前回の記事では設計審査(DR)についてまとめています。興味ある方は是非↓↓↓
設計と開発でプロセスを管理する設計審査(DR)とは?~QC検定攻略~
製品やサービスにおける、設計や開発のプロセスを確立し実施する事、そしてそれを維持していくにはどういったことが求められていくのでしょうか。 これらを計画し実施して得られた結果をレビューするDRとはどういった役割を持つのでしょうか。 今回は設計審査(DR)について例なども含めて解説していきます。 前回の記事では品質保証体系図と目的についてまとめています。興味ある方はぜひ↓↓↓ ...
検査の目的と考え方
組織外で自社の不良が発生してしまうと深刻なダメージを負います。これを未然に防止するために「検査」を行い根本的な不良を取り除きます。
ー検査とはー
サービスや製品において測定・検査などを行い、規定要求事項(ISOの基準)と比較して、適合・不適合を判断する活動
サービスや製品において測定・検査などを行い、規定要求事項(ISOの基準)と比較して、適合・不適合を判断する活動
また上記の「適合」が示すものは規定要求事項を満たしている事であり、満たされているものを「適合品」、満たされていないものを「不適合品」といいます。
検査の実施対象は大別して以下二つとなり、判定対象も異なってきます。
・製品 :「適合品」「不適合品」
・ロット:「合格」「不合格」
ここで検査の目的について触れていきます。
検査の目的とは
安定かつ優れた品質を顧客に提供するために、製品が基準内に収まっているか評価し、その評価を関連部署にフィードバックを行い、工程改善につなげる事
検査というのは単に検査を行って「適合・不適合」、「合格・不合格」を提示するのが目的でなく、検査によって根本的な不良の流出を防ぐことが第一の目的となります。
しかし検査による漏れが生じるとします。そうした場合、不良品情報を関連部署にフィードバックを行い、そもそも不良が発生しない工程を作っていく事、つまり「予防」を行っていく事が重要となります。
これらを常に意識していく事でモノづくりの永遠の課題である「検査なしのモノづくり」に近づいていきます。
検査で外部不良を防ぎ顧客の信頼獲得
不良は「外部不良」と「外部不良」に分類され顧客に迷惑がかかるのが外部不良となります。
・外部不良:市場に出てから不良が発覚
・内部不良:自社内の現場で不良が発覚
外部不良は顧客にとっては勿論悪影響を与えますが、自社においても顧客からの品質不信につながり信頼を失ってしまいます。
内部不良は製品が顧客の手に渡っていないので、信頼的視点においては影響はありませんが、不良品を破棄したり、再設計などで製造における単価が悪くなるのは確実なので内部不良は「内部不良は=コスト問題」という事になります。
仮に外部不良が発生するとしましょう。その場合生じるのが「売り上げ・利益・信頼」の減少です。
顧客は不良品を良品と交換することを要求してくることは間違いなく、場合によっては賠償金などを求められ想像以上の費用が必要となってきます。
また今どきはSNSなどの普及拡大により、そういった不祥事のネタはすぐに拡散され信頼の失墜に必ず繋がってきます。
もう一つ挙げるとすれば「社員のモチベーションの低下」です。
不良品を出してしまうとメディアなどで大きく取り上がられ、クレーム対応が増加し全社的な士気低下に繋がります。
こちらは金銭的ダメージは見かけ上はありませんが、この不良を出した不祥事をきっかけにリストラや早期退職、または自主的に転職する人が増えてくる可能性も低くありません。
人材を失うという事は今まで育ててきた「人財」を失う事であり、結果的に会社のコストを考えた時マイナスに働きます。
これらを回避するのに有用な手段が「検査」となります。
検査を徹底的に行うことによって仮に不良品を作ったとしても市場に出回ることがなければ、不祥事を未然に防止できます。
この未然防止策としては市場に出回る前の全製品に対して検査を確実に行うことです。
不良品の程度(命に係わる安全などは厳しい)にもよりますが、もし仮に不良品を出してしまったら、迅速に誠心誠意の謝罪をして、顧客からの要求というのを確実に形にすることで程度が緩和される場合もあります。
是正処置を迅速かつ確実に行い、今後の再発防止策を顧客側にも正確に伝えることで今後もビジネスパートナーとして関係を維持することが可能となります。
検査の取りこぼしは予防で補う
ここまで検査の重要性について述べてきました。検査をやれば不良品の発生を100%抑えることが出来るのかと言うと答えは「NO」です。
例えば95%の確率で不良品を検査で塞き止めることが出来るとします。一見高い数値ですが5%は何かの不良をもって市場に出回ってしまいます。
この検査では95%が最大なのでこの検査を続けていても永遠と5%づつ市場に不良品が流れることになります。
そこでこの流れを止めるのが予防となります。
検査とコストと不良率0の壁
予防に入る前に検査についてもう少し触れていきます。
検査はすごく優秀な手段というのは周知の事実かと思いますが、検査によって不良の発生を抑えることは出来ても100%抑えることは不可能です。
そもそもたった一つの対処で100%の壁を超えることはものづくりにおいてはあり得ませんが、、
しかし検査の質を何重にも厚く、何倍にも質を挙げれば99%ぐらいには押さえることが出来るのでは?と思うかもしれません。
因みにそれは可能であったとしてもほぼ不可能です。何故ならば人件費や検査費用(時間当たりの)が馬鹿にならないからです。
企業という大きな組織は営利目的で活動しています。ボランティアではありません。なので出来るだけコストを押さえたいというのは当たり前の事であり、このジレンマがいつまでたっても不良を作り続ける要因となります。
利益を求めるとき企業にはこんな葛藤が生まれます。(*あくまで最悪な例として挙げます)
見てわかるように顧客に対する「甘え」が生じています。これは完全にダメな例ですが、口に出さないだけでこのように楽観的にとらえている人は少なからずいると推測されます。
そこでこのような思考をもつ労働者がいても不良率を限りなく、0にするのが「予防」となります。
予防は不良を限りなく0にする
検査+予防をすることで不良を限りなく無くします。
やり方としては、検査によって得られた不良情報を製造現場や生産技術部に伝え、実際に不良が出ない工程そのものを作ってもらいます。
検査と予防を実際に生産ラインに組み込むとで最大の効力を発揮します。
因みに検査と予防のどちらが優先的なのかと言えば「検査」を優先しましょう。そもそも検査ありきの予防であって、検査で大まかな不良を取り除き、余ったものを予防で対処するという考え方です。
検査と予防とグラフの関係
さてここからは検査によって露呈した不良情報をもとに予防を行った際の効果の確認法について触れていきます。
検査は記事前半で説明させていただきましたが、基準内に収まっているかどうかを確認する事でしたね。
またここでの基準内というのは規格に収まっているのかという事を指します。
この規格を把握するtoolというのがQC7つ道具の一つである「ヒストグラム」になります。
QC検定3級のヒストグラムを5分解説!品質管理におけるヒストグラムの活用法とは
前回の記事ではQC7つの道具の一つである「チェックシート」についてご紹介いたしました。 チェックシートは標準かされた業務の効率を図ることはもちろん、改善箇所も把握しやすく、ぜひ検定を除いても理解を深めたいものでした。 下にリンクを貼っておきますのでまだご覧になっていない方、興味がある方は是非ご覧になってください。 こんにちは!インコです。 ...
ヒストグラムは規格上限値と規格下限値を設けて、その規格内であれば「良品」。規格外であれば「不良品」を一目で把握できる「シンプルかつ効率的に問題を認識」出来るtoolとして品質管理において重宝されています。
ヒストグラムの参考例として画像を用いて説明します。
ヒストグラムを活用するにあたって、初めに狙いというのを定め「狙い=平均値」というのを目指していきます。
そしてその平均値と狙いとの間にずれが生じた時、「ばらつき」が生じます。
基本統計量とは?グラフや平方和について ~QC検定攻略~
皆さんはばらつきについて解析するときどういった方法で求めますか? 分布の癖などを把握することにより、様々な事で改善のきっかけを探ることが出来ます。 今回の記事ではこれらを総じて表す基本統計量から標準偏差などについても触れていきたいと思います。 前回の記事ではデータの種類についてまとめています。興味ある方は是非↓↓↓ こんにちは!インコです! ...
そのばらつきによって規格を越したものが不良となります。
つまり検査によって露呈した不良情報をもとに予防を行い、ヒストグラムで確認します。そして規格外の値が検出されたら、再び検査を用いて不良を除き予防を行います。
この不良除去を行った二回目のヒストグラムの結果が以下になります。
不良を取り除いたことで良品のみが残り、全ての値が規格内に収まっています。
ここで「検査と予防の成果出たから終わり!」では駄目です。
上の図で問題個所を挙げると二か所あります。
1.平均値と狙いの値がずれている
2.規格ギリギリのものが多く不安定である
これらの課題を終えて初めて一連の流れが終わりを迎えます。
分かりやすいように極端に改善した図を以下に示します。
上限規格・下限規格からともに余裕のあるヒストグラムとなり「ばらつきも」消え綺麗な図となりました。
点線で多少の誤差を示していますが、これはそこまで追い求めなくて大丈夫です。100%を確立するのは無理難題であって100%に近づけることが大切となります。
検査と予防によって不良があったのを取り除き、規格にも余裕がある製品が作れた。
この事実を示せたのなら検査×予防×グラフの活用は完璧と言えるでしょう。
検査方法の種類
検査を行う際に重要なのは、その時行わなければいけない検査方法を的確に選択し、正確に活用していく事が求められます。
上記を完璧にこなすことで、異常品の発生を押さえたり、不適合品の市場流出を防いだり、次工程からの信頼、市場からの信頼を得ることが可能となります。
この検査方法の種類は大きく分けて3つに分類され、さらにそこから細分化していきます。
大別すると「生産プロセス」「判定方法」「実施方法」のつに分類され、そこから「受け入れ検査」「官能検査」「全数検査」と言うように細分化されます。
細分化された検査方法は10個に分類されこれらを徹底することで良質な品質の確立へ繋がります。
生産プロセスにおける検査方法
生産プロセスにおける検査の役割は大きく分類して3つあります。
・不良品の除去(合格の判定)
・記録を残す
・前工程にフィードバック
不良品の除去は「検査」の目的でもあるので大体想像はつくと思います。
では「記録を残す」とは何なのか。これは、前工程から引き継いだ製品を次工程で検査を行い、その結果を記録し、前工程にフィードバックすることです。
自工程で異常や不具合が出ずに、規格内に収まったとしても、後工程で装置上、材料上なんらかの問題が発生する可能性は十分あります。
そこで前工程に「問題のフィードバック」「改善の提案」を行います。この改善の提案は規模が大きいものから小さいものまで様々です。
規模が大きくなるにつれて必要とされる情報量も大きくなるのでより確実な検査結果が求められます。
この一連の流れで最も重要なのが「最終検査(出荷検査)」です。
最終検査は製品が設計品質に満たされているか確認することは勿論、お客様に届ける大切な製品に問題が起こらない様にきれいに梱包することが重要となります。
またこの最終検査の際、一人で確認を行うのではなく「ダブルチェック」などを用いて客観的視点で製品の確認を行うことで問題の市場流出を徹底的に押さえることが出来ます。
また最終検査で問題が起きた場合は、いったんリーダーやスタッフに事情を説明し、判断を任せるのが良いでしょう。
生産プロセスの検査の種類
生産プロセスにおける検査方法の役割は大きく分けて3つに分類されます。
・受入検査
・工程内検査
・最終検査(出荷検査)
生産プロセスにおける検査の目的としては、「ムダを省くこと」が挙げられます。
この無駄とは、「コスト」や「時間」の事を指し、3つの検査方法を活用することでうまくこれらを削減していきます。
上の図が生産プロセスにおける検査の一連の流れとなります。
ここでいう仕掛け品とは「未完成品」の事を指します。
受入検査
ー受入検査【JIS Z 8101:1981】-
提供された検査ロットを受け入れていいかどうかを判定するために行う検査
提供された検査ロットを受け入れていいかどうかを判定するために行う検査
購入した原材料や部品が入庫された際に行う検査です。
この検査を疎かにしてしまうと、いくら自社の現場に実力があっても、そもそものベースとなるものが悪ければ手の打ちようがありません。
ですので検査の入り口となる「受け入れ検査」はとても重要な検査となります。
受入検査とは?目的や購入仕様書・工程変更申請書・出荷検査成績書について。
皆さんは購入した製品や材料・商品などに対してどのような管理や検査を行っていますか? 長年の付き合いで信頼を置いているビジネスパートナーとの取引だとしても、検査を行うことは非常に大切な事となります。 そこで今回は検査の中の最初に登場する「受け入れ検査」についてまとめていきます。 受入検査の目的は勿論、「購入仕様書」「工程申請書」などにも触れていきたいと思います。 ...
工程内検査
ー工程内検査【JIS Z 8101:1981】-
工場内において半製品をある工程から次の工程に移動してもよいかどうかを行うために行う検査
工場内において半製品をある工程から次の工程に移動してもよいかどうかを行うために行う検査
工程内検査は前工程から次工程に工程を移動してもいいかを判定するための検査の事を指します。
この一連の流れは「後工程はお客様」という思想のもとに行われ、これは外部を対象とした検査と言うより、内部を対象とした検査となります。
工程内検査の意味とは?中間検査の目的などについて
製造業に携わる限り、工程の管理を行うことは避けては通れない必須事項です。 工程内管理を行う上で重要なのは、工程の検査を行い、後工程に異常品を渡さないことです。 「品質は工程内で作りこむ」という考えがありますが、この考えを形に出来る検査を「工程内検査」と言います。 今回の記事はこの「工程内検査」についてまとめていきます。 ...
最終検査
ー最終検査【JIS Z 8101:1981】-
完成した品物が、製品として要求事項を満たしているかどうかを判定するために行う検査
完成した品物が、製品として要求事項を満たしているかどうかを判定するために行う検査
製品に不備がないか、お客様の要求を満たしているかの最終確認を行います。
この確認を怠ると、万が一社会に影響力がある不良品が紛れていた時、手の打ちようがない事態に発展しますので「最後の砦」という認識で検査を行いましょう。
出荷検査の目的とは?最終検査の役割、重要性・信頼性について考える。
不良品が世に出回るか出回らないか、それをジャッジするのは受入検査でも工程内検査でもなく最終検査です。 この判断を誤ると、自身が想定していなかった大事になることは勿論、トラブルや多くの方々に迷惑をかけてしまう事態に見舞われます。 そうならないために最終検査はどういったことを意識して行い、また目的というのも明確にしていこうと思います。 ...
検査の判定方法
判定方法で分類する検査には3つの種類があります。
・計数抜取検査
・計量抜取検査
・官能検査
計(量・数)抜取検査はデータを元に評価を下すのに対して官能検査は人間の感覚のみで評価を行うのが大きな違いとなります。
計量抜取検査と計数抜取検査
【計数抜取検査】
適合数・不適合数をもとに判定
【計量抜取検査】
計量値などの測定値をもとに判定
適合数・不適合数をもとに判定
【計量抜取検査】
計量値などの測定値をもとに判定
二つを比較すると「データを元に判定する」のは同じですが、計数値抜取は「不適合数」が対象であり、計量抜取検査は「測定値」が対象となっています。
詳しいことは以下の記事にまとめています↓↓↓
計量値と計数値の違いについて考える。QC検定攻略
データとはひとくくりに言っても重さや長さと不適合品数は属するデータが異なります。 データには品質特性を表すものや、単位を表すものなど様々であり、意外とあやふやになりがちです。 そこで今回の記事はデータのとる目的から母集団やサンプルについてまとめてみました。 はじめに、そもそもなぜデータを取るのかというところから触れていきたいと思います。 データとは? ...
官能検査
官能検査とは
データや数値に頼らず、人間の感覚で判定を行う検査
データや数値に頼らず、人間の感覚で判定を行う検査
官能検査を検査に用いる事で検査コストを大幅に削減することが出来ます。
しかし想定機器などを用いらないので判定にばらつきが生じるなどのデメリットがあります。
官能検査の目的とは?メリット・デメリット・注意点・限度サンプルについて分かりやすく解説
品質管理における検査というのは、単に機械で判定するものではなく、人間の感覚で判断を下すものもあります。 機械で行う検査で数値化しにくいものは人間の感覚に判断をゆだねるしかなく、この検査方法を「官能検査」といいます。 今回は人間の「味覚」「聴覚」「嗅覚」を最大限に活かした検査方法である「官能検査」についてまとめてみました。 ...
実施方法による検査
実施方法による検査は言い換えれば、検査個数による検査方法とも言います。
この検査個数による検査方法は大別して4つに分類されます。
・全数検査
・抜取検査
・間接検査
・無視検査
これらには一長一短があり間違った判断で実施すると、不良の流出を防ぎきれない事態に陥ります。
それではひとつづつまとめていきます。
全数検査
【全数検査】
ロット中の全ての検査単位を調査し、適合か不適合かを判定
ロット中の全ての検査単位を調査し、適合か不適合かを判定
全数検査は言葉の通り製品すべてを対象として検査を行っていくので製造の品質は確かなものとなります。
しかし時間・コスト面を鑑みるとなかなかの財力と労力が必要とされます。
理想を言えばすべての検査を全数検査で行うことが「不良0」に近づく最善策なのは間違いないですが、理想と現実のギャップは厳しいものとされています。
全数検査を行うメリット・デメリットとは?特徴・目的などについて分かりやすく解説
工程で検査を行うとき、製品すべてに検査を行う「全数検査」が最も異常品の流出が少なく、流出数だけで見れば最善の手段といえます。 しかし多くの場合、この全数検査を全面的に実施する事は少なく、複数の検査方法を組み合わせて検査を進めていきます。 なぜ組織は不良品の流出を防げる全数検査を全面的に実施しないのでしょうか。 今回は全数検査の目的・特徴・メリット・デメリットについてまとめていきます。 ...
抜取検査
【抜取検査】
定めた検査方式を基準に、ロットからサンプルを抜きとって、そのサンプルを調査し、そのサンプルに対して「合格」「不合格」の判定
定めた検査方式を基準に、ロットからサンプルを抜きとって、そのサンプルを調査し、そのサンプルに対して「合格」「不合格」の判定
抜取検査の中には「破壊検査」も含まれ、これは内部の欠陥を調査するために破壊せざる得ない状況の時に活用されます。
また抜取検査には「ランダム」と「特定位置」に大別され、それぞれ意図が異なります。
抜取検査の基準とOC曲線との関係とは?規準型・調整型・連続生産型の特徴について分かりやすく解説
検査を実施するうえでは大別して全数検査と抜取検査に分類され、これらをうまく活用していく事で効率的かつ効果的に検査を進行させ、最終的な検査コストを削減することが可能となります。 本記事では実施検査の一つである「抜取検査」について分かりやすく解説していくとともに、OC曲線などの解説も行っていきます。 前回の記事では「全数検査」についてまとめていますので、興味ある方は是非↓↓↓ ...
間接検査
【間接検査】
メーカーが作成した「出荷検査成績書」で判定
メーカーが作成した「出荷検査成績書」で判定
間接検査は大きな枠組みでいえば「受け入れ検査」に含まれます。
つまり「出荷検査成績書」を活用して購入側の検査を省略することが出来ます。
無試験検査
【無試験検査】
信頼の元、検査を省略する検査
信頼の元、検査を省略する検査
今までの実績・対応など総合的な評価において、信頼がおけると判断した場合、サンプルの試験を省略する検査です。
無試験と一概に言っても完全な「無管理」という意味ではないので注意が必要です。
まとめ
検査方法にはそれぞれメリット・デメリットがあり適材適所で活用していく事で高いレベルの現場を築くことが出来る。
検査を行う際は精度やコスト面にも意識を向ける事で、真の現場改築に貢献できる。
いかがでしたか。
今回は検査方法の種類とそれぞれの目的についてまとめてみました。
次回は受入検査についてです。それでは!
QC検定3級を楽して受かりたい方にお勧めです。
QC検定3級【品質管理検定】の合格率・難易度・勉強法のすべて
ものづくりに携わるうえでものづくりと品質管理という役割は切っても切れない関係なのはご存じでしょうか? 最近は品質の不正などの多発により「品質」への関心が集められています。 その関心と共に注目されている自己摘発が そこで今回の記事はQC検定3級をした自身の経験をもとに攻略法・勉強法をお伝えできればと思います。 Point.1 こんな人にお勧めです ・勉強時間が足りないから要領よく学びたい ...
ブログランキング参加しています!

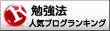
勉強法ランキング
FC2 Blog Ranking
わかりやすいまとめありがとうございます。
返信削除参考にしながら試験勉強を進めています。
1点、重大な誤字がありますので訂正いただければ幸いです。
「関節」検査は全て『間接』検査ではないでしょうか?
ご確認及び修正をお願いいたします
ご愛読ありがとうございます。
返信削除ご指摘いただきました箇所を修正させていただきました。
今後ともよろしくお願いいたします。